Основные размеры и условия для сборки двигателя ГАЗ-66, ГАЗ-53
Основные размеры и условия для сборки двигателя ГАЗ-66, ГАЗ-53
Все детали, поступающие на сборку, должны быть очищены от грязи, нагара и накипи, обезжирены, промыты и высушены.
Масляные каналы и отверстия в деталях должны быть прочищены, промыты под давлением и продуты сжатым воздухом.
Не допускается промывка деталей из алюминиевых и цинковых сплавов в щелочных растворах, применяемых для мойки стальных и чугунных деталей, так как алюминий и цинк растворяются в щелочах.
Все агрегаты, а также детали разобранных агрегатов при ремонте могут быть обезличены, за исключением следующих деталей:
— блока цилиндров и крышек коренных подшипников;
— шатуна и крышки шатуна;
— шестерен главной передачи;
— крышек подшипников дифференциала и картера главной передачи;
— правой и левой коробок сателлитов дифференциала. Допускается комплектование главной передачи из годных работавших или новых шестерен при условии обязательной проверки их зацепления на специальном приспособлении.
Отколы на зубьях шестерен и выкрашивание рабочей поверхности зубьев не допускаются.
Блок цилиндров и крышки коренных подшипников при разборке, контроле и сортировке не должны раскомплектовываться, так как они обработаны совместно и поэтому не взаимозаменяемы. Блоки цилиндров, поступающие на сборку, должны быть тщательно очищены от грязи и накипи, а масляные каналы — от шлама и стружки.
Гнезда вкладышей коренных подшипников должны быть расточены до номинального размера, если их размер и несоосность превышают допустимую величину. Чистота расточенных гнезд должна соответствовать классу 6-б по ГОСТ 2789—51, а максимальная их несоосность не должна превышать 0,02 мм.
При контроле, а также при растачивании гнезд момент затяжки болтов крепления, крышек коренных подшипников должен быть 11—12 кГм.
На поверхности расточенных гнезд вкладышей следы черноты не допускаются.
Втулки распределительного вала, запрессованные в блок цилиндров, должны быть расточены до номинального или одного из ремонтных размеров, приведенных в табл. 1.
Чистота расточенных поверхностей должна соответствовать классу 7 по ГОСТ 2789—5 1, а несоосность втулок не должна превышать 0,025 мм.
Непараллельность осей коленчатого и распределительного валов не должна превышать 0,04 мм на всей длине,
а расстояние между осями должно находиться в пределах 125,5 ± 0,025 мм.
Отклонение от перпендикулярности оси отверстий под гильзу цилиндра к оси коленчатого вала допускается в пределах 0,015 мм на длине 100 мм, а оси отверстий под толкатели к оси распределительного вала—не более 0,050 мм на длине 100 мм.
Чтобы обеспечить селективную сборку в новых блоках цилиндров, отверстия под толкатели рассортированы на две размерные группы.
Маркируют размерные группы маслостойкой краской на приливах под толкатели.
После обработки отверстий под толкатели ремонтных размеров их необходимо также сортировать на размерные группы. Маркировка размерных групп и ремонтные размеры отверстий под толкатели приведены в табл. 2.
Гильзы цилиндров
Гильзы цилиндров, устанавливаемые на один двигатель, должны быть номинального размера или расточены и хонингованы до одного общего для всех гильз ремонтного размера, указанных в табл. 3.
Овальность и конусность окончательно обработанных гильз не должна превышать 0,02 мм. Причем большее основание конуса должно быть в нижней части гильзы. Бочкообразность и корсетность не более 0,01 мм. Поверхность гильзы должна быть зеркально-блестящей без рисок и черноты, ее чистота должна соответствовать классу 9-а.
Чтобы обеспечить селективную сборку сопряжения гильза — поршень, на автомобильных заводах гильзы номинального размера сортируют на пять размерных групп. Размерные группы обозначают буквами русского алфавита, которые нанесены резиновой печаткой на шлифованной наружной поверхности гильз. С этой же целью гильзы, обработанные до ремонтного размера, также должны быть рассортированы на размерные группы.
Если овальность посадочной поверхности гильзы превышает допустимую величину 0,025 мм, то поверхность должна быть восстановлена осталиванием с последующей обработкой до номинального размера. При этом биение посадочной поверхности относительно внутренней поверхности гильзы не должно превышать 0,08 мм, а непараллельность осей, указанных поверхностей не должна превышать 0,02 мм на длине 100 мм.
Поршни и поршневые пальцы
Для авторемонтного производства выпускают поршни номинального и трех ремонтных размеров.
Для обеспечения подбора по гильзам поршни рассортированы на пять размерных групп, которые обозначены буквами русского алфавита. Обозначение размерной группы выбито на днище поршня. Размерные группы поршней номинального и ремонтного размеров, а также их обозначения приведены в табл. 4.
По диаметру отверстия под поршневой палец поршни рассортированы на четыре размерные группы. Группы маркируют маслостойкой краской на наружной поверхности бобышек поршней. Размерные группы отверстия под поршневой палец и их маркировка приведены в табл, 5.
Юбка поршня выполнена овальной и имеет конусность. Большая ось овала расположена в плоскости, перпендикулярной оси поршневого пальца, а конусность юбки в этой же плоскости должна составлять 0,013—0,038 мм. Наибольший диаметр конуса должен быть в нижней части юбки.
При капитальном ремонте двигателей применяют поршневые пальцы только номинального размера, которые рассортированы на четыре размерные группы. Размерные группы поршневых пальцев номинального размера и их маркировка приведены в табл. 6.
Поршневые кольца
Поршневые кольца выпускают номинального и трех ремонтных размеров, приведенных в табл. 7.
Из трех колец, устанавливаемых на один поршень, два (второе компрессионное и маслосъемное) должны быть покрыты полудой, а верхнее компрессионное — хромом.
При проверке в кольцевом калибре соответствующего размера просвет между поршневым кольцом и калибром не допускается. Упругость компрессионных колец, сжатых стальной лентой до зазора в стыке 0,3 ∕0,5 мм, должна быть 1,75 — 2,50 кГ, а маслосъемных — 1,5 — 2,2 кГ.
Шатуны
Шатун и крышка шатуна при разборке, контроле и сортировке не должны раскомплектовываться, так как они не взаимозаменяемы.
Допускается восстановление отверстия нижней головки шатуна осталиванием с последующей обработкой до номинального размера. Перед обработкой нижней головки гайки шатунных болтов должны быть затянуты динамометрическим ключом. Момент затяжки — 6,8 — 7,5 кГм.
Втулки, запрессованные в верхнюю головку шатунов, должны быть расточены до номинального размера. Перед растачиванием втулки должны быть проглажены брошью.
Чистота обработанных поверхностей во втулке и нижней головке шатуна должна соответствовать классу 8-б.
После растачивания овальность и конусность верхней головки шатуна не должны превышать 0,005 мм, нижней — 0,008 мм.
Непараллельность осей отверстий верхней и нижней головок шатуна — не более 0,03 мм на длине 100 мм, оси отверстий верхней и нижней головок шатуна должны лежать в одной плоскости, отклонение не более 0,04 мм на длине 100 мм.
Перпендикулярность торцовых поверхностей нижней головки относительно оси отверстия — не более 0,05 мм.
У шатунов, поступающих на сборку двигателя, расстояние между осями нижней и верхней головок должно быть 155,95 — 156,05 мм.
Для обеспечения возможности селективной сборки шатуна с поршневым пальцем шатуны должны быть рассортированы на группы по размеру отверстия в верхней головке. Каждую группу шатунов маркируют маслостойкой краской определенного цвета. Маркировка шатунов приведена в табл. 8.
Коленчатый вал
У коленчатых валов, поступающих на сборку, масляные каналы и грязеуловители должны быть тщательно очищены от шлама.
Шатунные и коренные шейки должны быть номинального или одного из ремонтных размеров, указанных в табл. 9.
При шлифовании шатунных шеек радиус кривошипа должен быть сохранен номинальным.
Для одноименных шеек разные ремонтные размеры не допускаются.
Овальность и конусность шеек коленчатого вала не должны превышать 0,01 мм.
Чистота поверхности шеек должна соответствовать 9-му классу.
Длина передней коренной шейки должна быть в пределах 30,45—30,90 мм. Длина шатунной шейки — 52,0—52,2 мм.
Радиусы галтелей шатунных шеек должны быть в пределах 1,2—2,0 мм, коренных — 1,2—2,5 мм.
При вращении вала, установленного в призмы на крайние коренные шейки, биение не должно превышать:
— для средних коренных шеек — 0,02 мм;
— для шейки под распределительную шестерню — 0,03 мм;
— > ступицу шкива вентилятора — 0,04 мм;
— > > задний сальник — 0,04мм;
— фланца по торцу — 0,04 мм.
Не параллельность осей шатунных и коренных шеек — не более 0,012 мм на длине каждой шейки.
Коренные и шатунные вкладыши
Тонкостенные вкладыши подшипников коленчатого вала должны быть полностью взаимозаменяемы, и обеспечивать без подбора необходимые для нормальной работы двигателя посадки в сопряжениях подшипников.
Не допускается наличие трещин и откалывание антифрикционного слоя от стальной ленты у шатунных и коренных вкладышей.
Забоины и царапины на рабочей поверхности не допускаются.
На обратной стороне вкладыша допускаются царапины глубиной не более 0,1 мм в количестве не более трех.
Острые кромки и заусеницы на стыках вкладыша должны быть зачищены. Забоины, царапины и коррозия на плоскостях стыков вкладышей не допускаются. Зачистка стыков для выведения этих дефектов не допускается.Фиксирующий выступ вкладыша не должен иметь повреждений. Ремонт вкладышей перезаливкой антифрикционного слоя не допускается.Номинальный и ремонтные размеры вкладышей приведены в табл. 10.
Маховик
Рабочая поверхность маховика должна быть гладкой, ее чистота после обработки должна соответствовать 9-му классу. Маховик должен подвергаться статической балансировке. Величина допустимого дисбаланса не должна превышать 35 гсм. При балансировке сверлить отверстие диаметром 11 мм на радиусе 156 мм на глубину 18 мм.Максимальное биение рабочей поверхности не должно превышать 0,1 мм.Размеры отверстий под болты крепления маховика не должны превышать 12,30 мм.
Распределительный вал
Опорные шейки распределительного вала должны быть номинального или одного из ремонтных размеров, приведенных в табл. 11.
Овальность и конусность опорных шеек — не более 0,010 мм, Взаимное биение опорных шеек и шейки под шестерню — не более 0,020 мм.
Биение цилиндрической части кулачков относительно шеек — не более 0,05 мм.
Чистота обработки поверхности опорных шеек должна соответствовать классу 9-б.
При установке вала на крайних опорных шейках биение промежуточных шеек не должно превышать 0,05 мм.
Толкатели
Толкатели по наружному диаметру должны быть номинального или одного из ремонтных размеров, приведенных в табл. 12.Овальность, конусность и огранка наружной поверхности толкателя — не более 0,007 мм.Твердость наружной сферической поверхности RC— 60.На поверхности толкателя не допускаются трещины, риски, черновины и прижоги.
Головка цилиндров
Головка цилиндров, поступающая на сборку, должна быть тщательно промыта, рубашка охлаждения должна быть очищена от накипи и грязи, масляные каналы — от шлама, а выпускные каналы — от нагара.
Запрессованные в головку блока направляющие втулки клапанов должны быть номинального или одного из ремонтных размеров и маркированы краской. Размеры втулок и их маркировка указаны в табл. 13.Расстояние от верхнего торца направляющей втулки до плоскости головки должно быть равно 24 мм.Седла впускных и выпускных клапанов должны быть шлифованы под 45° к оси направляющих втулок. Ширина рабочей фаски седла должна быть 1,5 ± 2,0 мм. Биение конических поверхностей всех седел клапана относительно осей отверстий направляющих втулок клапанов — не более 0,025 мм. Запрессованные в головку цилиндров направляющие втулки клапанов по наружному диаметру могут быть номинального размера или ремонтного (увеличенного на 0,25 мм).
Впускной и выпускной клапаны
Диаметры стержней клапанов должны быть номинального или одного из ремонтных размеров, приведенных в табл. 14. Рабочая фаска головки клапана должна быть шлифована под углом 45° к оси стержня. Чистота рабочей поверхности фаски после шлифования должна соответствовать 8-му классу. Биение рабочей поверхности фаски относительно стержня клапана не более 0,03 мм.
Впускная труба
У впускной трубы, поступающей на сборку, рубашка охлаждения должна быть очищена от грязи и накипи, а впускные каналы от нагара. Поверхности разъема с головками цилиндров должны быть плоскими — отклонение в пределах 0,1 мм не более.
Трубу нужно подвергнуть испытанию водой под давлением 3 – 4 кГ/см2.
2.4.1. ГАЗ. Эксплуатация, обслуживание и ремонт автомобилей ГАЗ-53А и ГАЗ-66. Определение технического состояния и ремонт отдельных деталей и узлов двигателя. Кривошипно-шатунный механизм — «ВАЖНО ВСЕМ»
Все поверхности трения в блоке цилиндров, кроме направляющих толкателей, снабжены легкосъёмными сменными втулками (гильзы цилиндров, вкладыши коренных подшипников, втулки подшипников распределительного вала). Такая конструкция делает блок практически неизнашиваемым.
Гильзы цилиндров мокрые, непосредственно омываемые водой. Для увеличения коррозийной стойкости гильзы в верхней части её запрессована малая гильза, изготовленная из кислотоупорного легированного чугуна, наружная поверхность гильзы покрыта кадмием.
В результате естественного износа поверхность зеркала гильзы приобретает по длине форму неправильного конуса, а по окружности — форму овала. Наибольшей величины износ достигает в верхней части гильзы, против верхнего компрессионного кольца; наименьший — в нижней части.
Износ гильзы 0,3 мм является предельно допустимым.
Все гильзы одного блока цилиндров должны иметь размер в пределах одной размерной группы. Максимальная овальность и конусность гильзы допускаются не более 0,02 мм.
Гильзы после третьего ремонтного размера (табл. 3) должны быть заменены новыми, номинального размера.
Наименование размера | Увеличение размера | Диаметр гильзы |
Номинальный | 0,0 | 92,00 |
1-ый ремонтный | 0,5 | 92,50 |
2-ой ремонтный | 1.![]() |
93,00 |
3-ий ремонтный | 93,50 |
Направляющие толкателей. Замена толкателей клапанов вызывается увеличением зазоров между толкателем и его направляющей в блоке цилиндров в результате износа. Допустимый предельный размер направляющих не должен превышать 25,05мм.
В запасные части выпускают толкатели только номинального размера. Поэтому при износе направляющих в блок цилиндров необходимо вставить ремонтные втулки.
Ремонтные втулки изготовляют из алюминиевого сплава АЛ4 с термической обработкой: нагрев до температуры 175±5°С, выдержка 5—15ч на охлаждение на воздухе. Размеры втулок: наружный диаметр 30 Перед запрессовкой втулок блок цилиндров нагреть до температуры 90—100°С. После запрессовки втулки развернуть до диаметра 23+0,023 мм,
Втулки распределительного вала поступают в запасные части полуобработанными. Кроме развертки или расточки внутреннего диаметра они не требуют никакой обработки.
0кончательно внутренний диаметр втулок растачивают или развертывают после запрессовки в блок цилиндров. Чтобы обеспечить соосность втулок, их следует обрабатывать одновременно при помощи длинной и достаточно жёсткой борштанги с насаженными на неё по числу опор резцами или развёртками.
Борштангу устанавливают с базировкой на отверстия для вкладышей коренных подшипников. При этом непараллельность осей распределительного и коленчатого валов должна быть не более 0,05мм на всей длине блока цилиндров, а расстояние между указанными осями 125±0,025 мм.
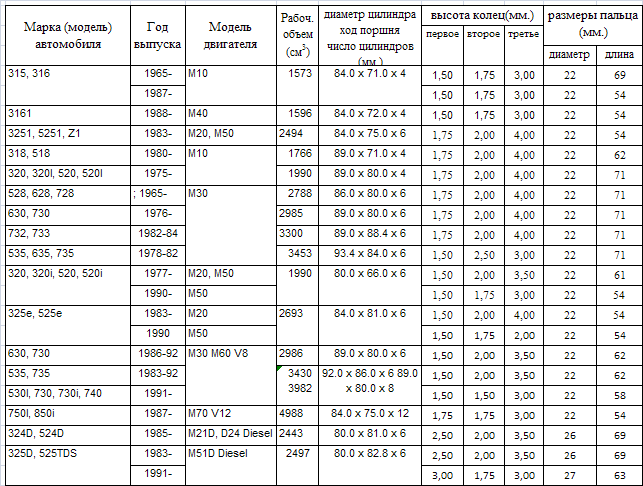
Поверхность обработанных втулок должна быть чистой и гладкой.
Головки цилиндров. На двигателе устанавливают две головки цилиндров. Каждая головка центрируется двумя фиксирующими втулками-штифтами, запрессованными в блок цилиндров.
В головках цилиндров запрессованы направляющие втулки и сёдла клапанов.
Втулки клапанов — металло-керамические. Внутренний диаметр втулки впускного клапана 9+0,022
Допустимый износ отверстия направляющих втулок клапанов не должен превышать 0,05 мм. При большем увеличении внутреннего диаметра втулки её следует заменить,
Для запасных частей клапаны выпускают стандартного размера, а втулки — с внутренним диаметром, уменьшенным на 0,3 мм, т.

Изношенную втулку выпрессовывают при помощи выколотки. Новую втулку запрессовывают при помощи упорной оправки со стороны коромысел. Втулка над плоскостью под пружину клапана должна выступать не более чем на 22 мм. После запрессовки отверстие втулки клапана развертывают до соответствующего стандартного размера.

Рис.19. Замер концентричности седла и отверстия втулки клапана
При замене седла клапанов удаляют при помощи твердосплавных зенкеров.
Перед установкой седла ремонтного размера его гнездо в головке цилиндров растачивают до размеров: для седла впускного клапана 49,25+0,027 мм и выпускного — 38,75+0,027 мм.
Перед запрессовкой в головку цилиндров седла и направляющие втулки клапанов охлаждают в твердой двуокиси углерода (сухом льде), а головку цилиндров нагревают до 160—175°С. Холодные седла и втулки при сборке должны входить в гнезда нагретой головки цилиндров свободно или с небольшим усилием. Под лёгкими ударами молотка по оправке седло и втулка клапана должны сесть на место. Ни в коем случае нельзя заколачивагь седло или втулку с большим усилием, так как при этом нарушается посадка, и в дальнейшем при работе двигателя седло или втулка могут выпасть из своего гнезда. Операцию по установке седел и втулок в головку цилиндров необходимо выполнять быстро.
Рабочие фаски вновь установленных седел прошлифовать концентрично отверстиям в направляющих втулках клапанов. Для этого используют специальное приспособление. Разжимную оправку устанавливают в обработанное отверстие втулки, и хвостовик оправки служит осью для шлифовального круга (привод от электродвигателя) с фаской под углом 45°. При шлифовке должна быть обеспечена концентричность рабочей фаски седла и отверстия втулки клапана 0,03 мм (по индикатору).
Поршни изготовлены из высококремнистого алюминиевого сплава. Для лучшей приработки они покрыты тонким слоем олова.
Для обеспечения индивидуального подбора поршней по цилиндрам каждый из ремонтных размеров делится на размерные группы.
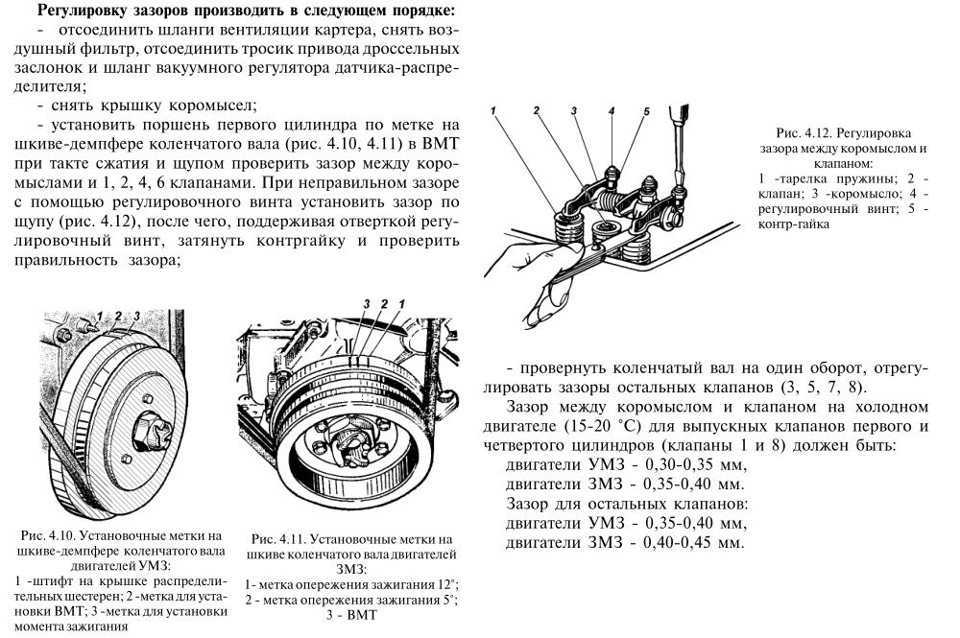
Некруглость отверстий в поршне под палец допускается не более 0,0025 мм.
Предельный зазор в соединении палец-поршень должен быть не более 0,1 мм.
Замена поршней вызывается увеличением зазора между поршнем и гильзой цилиндра. Увеличение зазора происходит в основном из-за износа стенки цилиндра. Износ юбки поршня бывает обычно незначительным. В поршне с увеличенными отверстиями ставят поршневые пальцы ремонтного размера с предварительной развёрткой отверстий под ремонтный размер. Для обеспечения необходимой посадки отверстие в поршне обрабатывать с допуском — 0,005 — 0,010 мм от соответствующего размера. При этом следует иметь в виду, что несоосность этих отверсгий не должна быть более 0,05 мм на длине 100 мм, неперпендикулярность оси поршня также не более 0,05 мм на длине 100 мм.
Основным параметром, определяющим необходимость замены поршней, является износ торцов канавок под поршневые кольца.
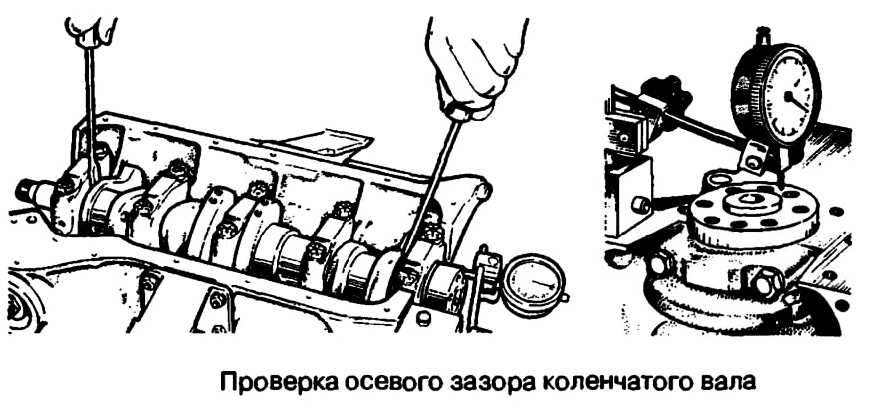
При большом износе поршневых канавок замена одних колец не дает положительного результата. Поэтому при зазорах между торцом кольца и канавкой в поршне выше 0,15 мм необходимо заменять и кольца, и поршни.
Поршни заменяют с подбором их при помощи ленты-щупа по гильзам, в которых они будут работать.
Ленту-щуп закладывают между гильзой и поршнем со стороны, противоположной прорези на юбке поршня, по всей его длине. Усилие протягивания ленты-щупа 3 — 4 кГ для новых гильз и поршней и 2 — 3 кГ для гильз и поршней, бывших в употреблении. Подбирают поршни без поршневых пальцев при +20°С. Если температура выше или ниже +20°С, то усилие протягивания ленты должно быть ближе к верхнему пределу при температурах +20°С и ближе к нижнему пределу при температурах ниже +20°С. После подбора поршни маркируют в соответствии с номерами цилиндров, к которым они подобраны.
Поршневые кольца изготавливают из серого чугуна индивидуальными отливками некруглой формы.
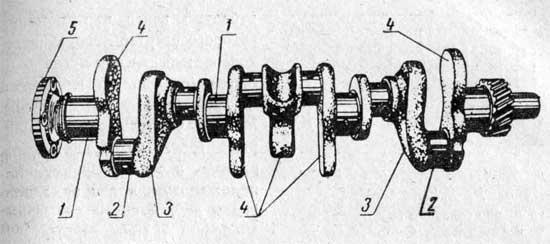
Цилиндрическую поверхность верхнего компрессионного кольца покрывают пористым хромом, остальные кольца — слоем олова.
Упругость компрессионных колец, сжатых стальной лентой до зазора в стыке 0,4 мм, должна быть не менее 1,75 — 2,5 кГ, а маслосъёмного кольца — 1,6 — 2,2 кГ.
Выпускаемые заводом кольца ремонтных размеров отличаются от стандартных только наружным диаметром.
Кольца того или иного размера предназначаются также для установки в изношенные цилиндры ближайшего меньшего ремонтного размера (в пределах 0,5 мм) путем подпиливания их стыков до получения нужного зазора в замке (0,3 — 0,5 мм).
Зазор подгоняют обязательно на том цилиндре, в котором будет работать данное кольцо. При подгонке необходимо следить за тем, чтобы кольцо не было перекошено в цилиндре, а лежало в плоскости, перпендикулярной его оси. Подпиливать стыки колец надо так, чтобы их плоскости при сжатии кольца были параллельны.
Поршневые кольца располагаются в поршневых канавках с достаточным зазором во избежание их заедания и пригорания.
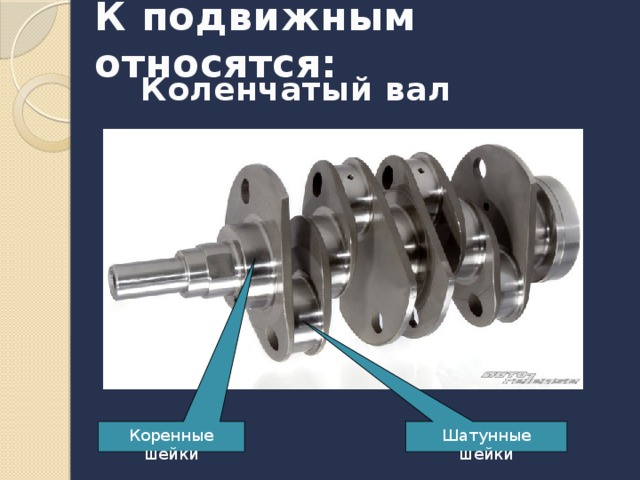
Если боковой зазор недостаточен, то следует, убедившись сначала, что торцы поршневых канавок свободны от забоин и заусенцев, слегка потереть кольцо о лист мелкозернистой наждачной бумаги, положенной на проверочную плиту, и делать это до тех пор, пока между торцом кольца и стенкой канавки можно будет завести щуп толщиной 0,05 — 0,08 мм.
Если же зазор между кольцами и стенками канавок будет больше допустимого (0,15 мм), то необходимо заменить как поршневые кольца, так и сам поршень.
Поршневые пальцы — стальные, пустотелые. Допускаемая нецилиндричность пальца — не более 0,0025 мм. Разница в весе пальцев, входящих в один комплект, не должна превышать 2 г.
В запасные части поршневые пальцы поставляют четырех размеров.
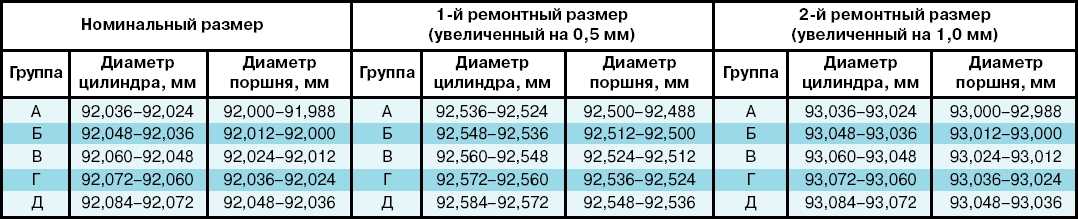
Стопорные кольца поршневого пальца должны сидеть в канавках поршня с некоторым натягом и не должны проворачиваться от руки.
Шатуны — стальные, кованые, двутаврового сечения. Нижнюю головку шатуна обрабатывают в сборе с крышкой, и поэтому при разборке, контроле и сборке шатун и крышку сохранять в комплекте. Не рекомендуется также обезличивать комплект шатунов с одного двигателя, так как на заводе-изготовителе шатуны подбирают по весу. Разница в весе шатунов одного комплекта не должна превышать 8 г.
В шатунах изнашиваются втулки верхних головок и вкладыши подшипников нижних головок. Предельный зазор в соединении поршневой палец — шатун должен быть не более 0,10 мм. Ремонт шатуна в основном сводится к замене втулки и развертыванию её отверстия до необходимого размера (номинального или ремонтного) и замене шатунных вкладышей.
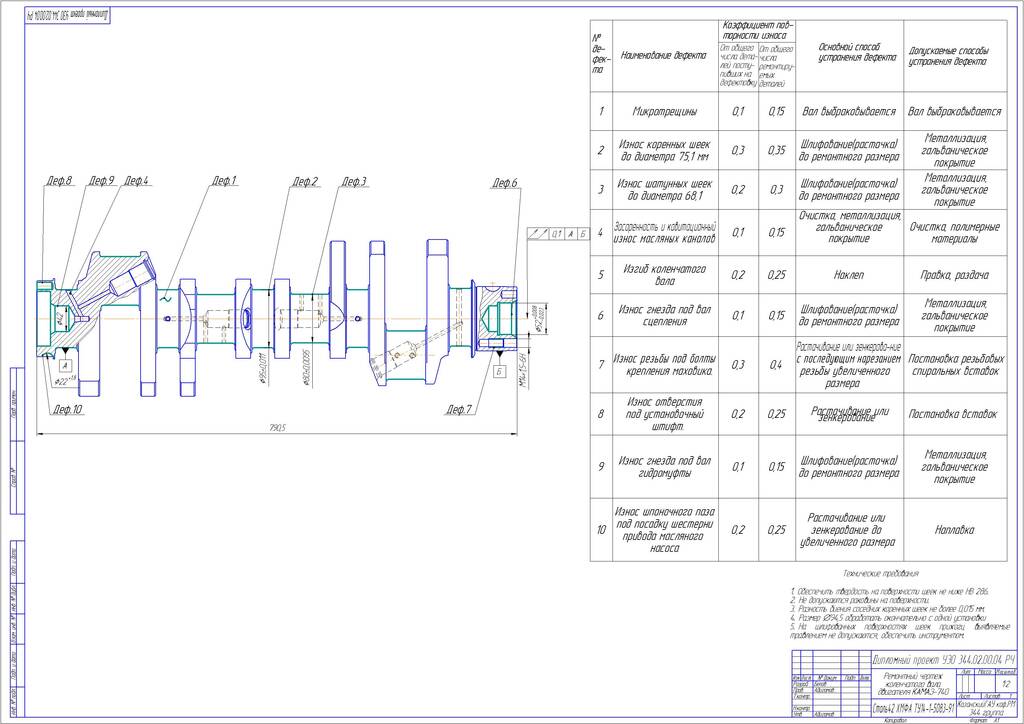
Необходимая посадка пальца в шатуне получается, если обработать отверстие под палец с допуском +0,005 мм от соответствующего размера.
После окончательной обработки нецилиндричность отверстия втулки допускается не более 0,0025 мм. Шатун обрабатывают в кондукторе соответствующей конструкции. Расстояние между осями отверстий верхней и нижней головок шатуна должно быть 168+0,05 мм; еспи отверстий должны быть параллельны друг другу в двух взаимно перпендикулярных плоскостях в пределах 0,04 мм на длине 100 мм.
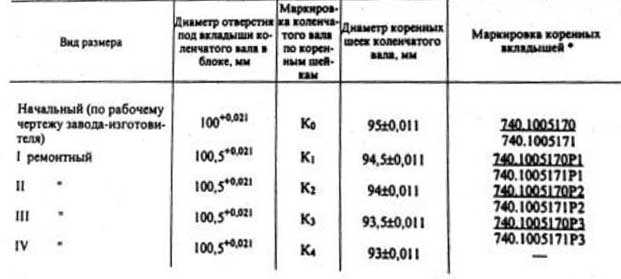
В процессе эксплуатации двигателя шатун подвергается изгибу и кручению. Если непараллельность осей не превышает 0,08 мм на дливе 100 мм в двух взаимно перпендикулярных плоскостях, то такие шатуны могут быть восстановлены правкой. Если непараллельность больше 0,08 мм, то такой шатун заменяют.
При правке шатун сначала закручивают несколько больше того, чем это необходимо для ликвидации деформации, а затем раскручивают в обратном направлении, пока оси головок шатуна не станут параллельными. Такой метод правки повышает стойкость шатуна против деформации во время дальнейшей работы его в двигателе.
Коленчатый вал отлит из магниевого чугуна. Коленчатый вал статически и динамически сбалансирован. Допустимый дисбаланс коленчатого вала — не более 15 Гсм.
Диаметр коренных шеек — 70 мм, шатунных — 60 мм, Коренные и шатунные шейки выполнены полыми в литье. Полости шатунных шеек герметически закрыты пробками и используются для дополнительной очистки масла, подающегося к шатунным подшипникам.
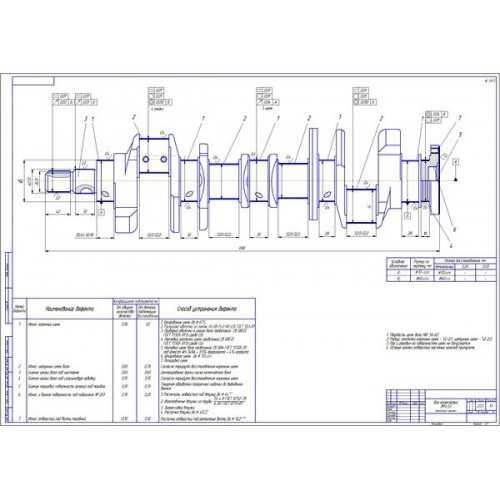
В процессе работы коренные в шатунные шейки коленчатого вала в результате износа теряют свою первоначальную геометрическую форму. Это снижает работоспособность как подшипников коленчатого вала, так и всего кривошипно-шатунного механизма.
Перекосы, которые возникают в этом случае в кривошипно-шатунном механизме, вызывают повышенный износ зеркала цилиндров и поршневых колец, они могут служить также причиной выталкивания поршневым пальцем стопорных колец из своих канавок и выхода поршневого пальца из поршня.
Износ коренных шеек более интенсивен, чем шатунных. Шейки коленчатого вала в результате износа принимают форму неправильного конуса и овала.
Если конусность или овальность шеек коленчатого вала выше 0,05 мм, то вал необходимо перешлифовать на ближайший ремонтный размер. Ремонтные размеры шеек коленчатого вала определяются размерами вкладышей, поставляемых в запасные части. Таких размеров семь.
Все шатунные или коренные шейки коленчатого вала следует перешлифовать под один ремонтный размер.
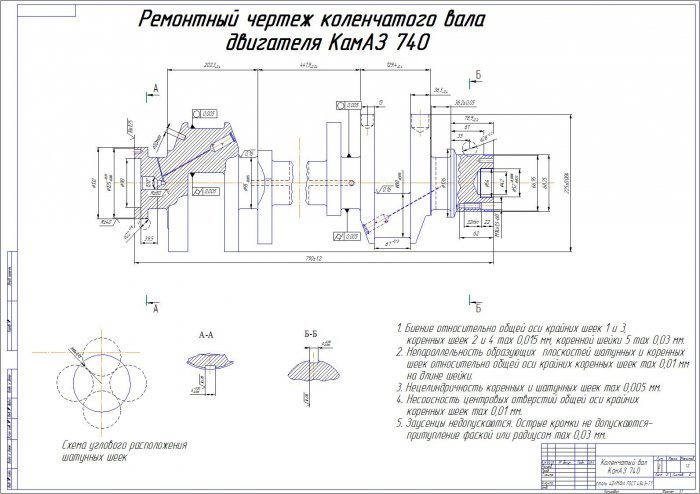
Для обеспечения необходимого зазора в подшипниках шейки коленчатого вала как шатунные, так и коренные шлифуют с допуском — 0,013 мм от соответствующего ремонтного размера.
После шлифования шейки коленчатого вала полируют до чистоты не ниже 9в класса.
После ремонта все масляные каналы и полости в коленчатом валу тщательно промывают и продувают сжатым воздухом.
Подшипники коленчатого вала. Коренные подшипники коленчатого вала имеют тонкостенные вкладыши, выполненные из триметаллической ленты: стальная основа, металло-керамическнй подслой (медь с никелем) и слой антифрикционного сплава СОС-6-6.
Шатунные подшипники имеют тонкостенные вкладыши, изготовленные из биметаллической ленты: стальная основа и антифрикционный алюминиевый сплав.
Тонкостенные вкладыши изготовлены с высокой степенью точности, в поэтому их ремонт или какая-либо подгонка с опиловкой или шабровкой недопустимы.

Маркировка ремонтных размеров вкладышей нанесена на стальной поверхности вкладыша. Вкладыши номинальных размеров маркировки не имеют.
Между шейкой коленчатого вала и вкладышем подшипника должен быть зазор: для коренных 0,026 — 0,071 мм и 0,030 — 0,067 мм для шатунных подшипников.
Величину радиального зазора можно проверить при помощи контрольных щупов, выполненных из медной или латунной фольги толщиной 0,025; 0,050; 0,075 и 0,1 мм, нарезанных в виде полосок шириной 6 — 7 мм и длиной несколько меньше, чем ширина вкладыша. Кромки щупов должны быть зачищены для исключения порчи поверхности вкладыша.
Радиальный зазор проверяют следующим образом.
- С проверяемого подшипника снимают крышку с вкладышем и на поверхность вкладыша укладывают предварительно смазанный маслом щуп минимальной толщины (0,025 мм).
- После постановки крышки на место и затяжки её (момент затяжки для коренных 11 — 12 кГм, для шатунных 6,8 — 7,5 кГм) делают попытку провернуть вал, при этом крышки остальных подшипников ослабляют; если вал вращается слишком легко, то, значит, зазор больше 0,025 мм.
- После этого щуп заменяют на следующий по толщине до тех пор, пока для провёртывания вала потребуется значительное усилие.
Толщина щупа, при котором вал проворачивается с ощутимым усилием, принимается равной фактическому зазору в подшипнике. Предельный зазор в подшипниках коленчатого вала не должен превышать 0,15 мм.
Во избежание повреждения поверхности вкладыша при проверке зазора при помощи щупов коленчатый вал следует повёртывать на угол не более 60 — 90°.
МАЗ. Ремонт, обслуживание и эксплуатация автомобилей семейства МАЗ → 3.4. Трансмиссия автомобилей МАЗ. Ведущие мосты. Устройство.
МАЗ. Ремонт, обслуживание и эксплуатация автомобилей семейства МАЗ → 3. 1.2. Трансмиссия автомобилей МАЗ. Сцепление и его привод. Ремонт
МАЗ. Ремонт, обслуживание и эксплуатация автомобилей семейства МАЗ → 2.1.1.2 Ремонт кривошипно-шатунного и газораспределительных механизмов двигателей автомобилей МАЗ.
МАЗ. Ремонт, обслуживание и эксплуатация автомобилей семейства МАЗ → 2.1.4.2. Ремонт системы питания двигателя автомобилей МАЗ
МАЗ. Ремонт, обслуживание и эксплуатация автомобилей семейства МАЗ → 2.1.4. Система питания двигателя автомобиля МАЗ.Устройство.
Характеристики, диаметр цилиндра и ход поршня, головки цилиндров, характеристики кулачков и многое другое
Двигатель LC9 представляет собой малоблочный алюминиевый двигатель 4-го поколения объемом 5,3 л, который использовался в грузовиках и внедорожниках GM в период с 2007 по 2011 год.
В маркетинговых целях он был также известен как Vortec 5300. Приведенные здесь характеристики и информация относятся к стандартному двигателю LC9.
Механически похожие двигатели General Motors LS и Vortec на базе LS заведены почти на каждую ветвь генеалогического древа GM: Chevy, Pontiac, GMC, Cadillac, Buick — черт возьми, даже Saab, Hummer и Isuzu получили некоторые ЛС любовь.
Поскольку двигатели LS и Vortec настолько распространены, они стали лучшими двигателями современной эпохи.
Эти двигатели способны развивать большую мощность и хорошо реагируют на модернизацию, такую как турбины, нагнетатели, головки блока цилиндров с высоким расходом, системы впуска, кулачки и закись азота.
Рынок послепродажного обслуживания развит, доступны двигатели в ящиках , а бывшие в употреблении двигатели часто дешево закупаются на свалках.
Компания Summit Racing создала серию подробных руководств для каждого двигателя семейства LS, чтобы производители и тюнеры двигателей могли иметь удобный справочник для своих проектов.
Это специальное руководство предназначено для двигателя GM LC9 5,3 л.
Дополнительные руководства по спецификациям двигателей LS и информацию, связанную с LS, можно найти здесь.
(В подготовке этой статьи участвовали Пол Сперлок и Брайан Наттер из компании Summit Racing. )
Характеристики двигателя LC9 Степень сжатия 9,9:1 (2007-09), 9,6:1 (2010-11) Номинальная мощность 302-315 л.с. Номинальный крутящий момент 330–338 футо-фунтов.
Приложения LC9
Приложения LC9 | |||
---|---|---|---|
Восьмая цифра VIN | Год | Марка | Модель |
3 | 2007-11 | Шевроле | Лавина |
3 | 2007-11 | Шевроле | Сильверадо 1500 |
3 | 2007-11 | GMC | Sierra 1500 |
3 | 2007-11 | Шевроле | Пригородный |
3 | 2007-11 | GMC | Юкон XL |
3 | 2009-10 | GMC | Юкон |
3 | 2009-11 | Шевроле | Тахо |
Технические характеристики блока цилиндров LC9
Спецификации блока LC9 | |
---|---|
Литейный номер | 125771048, 12601900, 12569513, 12568573 |
Материал | Алюминий |
Рабочий объем | 5,3 л / 325 c.![]() |
Диаметр отверстия | 3,780 дюйма |
Ход | 3,622 дюйма |
Высота платформы | 9,240 дюйма |
Расстояние между отверстиями | 4,400 дюйма |
Расположение упорного подшипника | #3 Основной |
Тип основной крышки | 6 болтов |
Диаметр отверстия основного корпуса. | 2,751 дюйма |
Диаметр отверстия корпуса кулачка. | Отверстие 1/5 = 2,346 дюйма Отверстие 2/4 = 2,326 дюйма Отверстие 3 = 2,307 дюйма |
Осевая линия кулачка и кривошипа | 4,914 дюйма |
Вращающийся узел LC9
ЛК9Технические характеристики вращающегося узла | |
---|---|
Материал поршня | Заэвтектический литой алюминиевый сплав |
Поршневой тип | Плоский верх (2007-09), Плоский верх с предохранительными клапанами (2010-11) |
Объем поршня | 0cc (2007-09), 3cc (2010-11) |
Диаметр штифта для запястья.![]() | 0,9431 дюйма (полностью плавающий) |
Материал шатуна | Металлический порошок |
Тип шатуна | Двутавровая балка |
Длина шатуна | 6,098 дюйма |
Отверстие корпуса шатуна | 2,225 дюйма |
Болты шатуна | M9 x 1 x 43 |
Соединительный стержень Номер детали | 12649190 |
Номер отливки шатуна (последние три цифры) | 143 |
Материал коленвала | Чугун |
Номер детали коленчатого вала (последние 3 цифры) | 12588614 |
Номер отливки коленчатого вала (последние три цифры) | 216 |
Диам.![]() | 2,559 дюйма |
Диаметр шейки коленчатого вала. | 2,100 дюйма |
Колесо Reluctor | 58x |
Головки цилиндров LC9
Технические характеристики головки блока цилиндров LC9 | |
---|---|
Литейные номера | 799, 243 |
Материал | Алюминий |
Объем камеры сгорания | 65cc |
Форма впускного отверстия | Собор |
Объем впускного патрубка | 210 куб. см |
Форма выпускного отверстия | D-образное отверстие |
Объем выхлопной трубы | 75cc |
Диаметр впускного клапана | 2000 дюймов |
Диаметр выпускного клапана | 1,575 дюйма |
Тип болта головки блока цилиндров | Момент текучести (TTY) |
Размер болта головки блока цилиндров | (10) M11 x 2 x 100, (5) M8 x 1,25 x 45 |
Спецификации распредвала LC9
Годы | 2007-09 | 2010-11 |
---|---|---|
Номер детали | 12593207 | 12625436 |
Длина @ 0,050 дюйма (внутр.![]() | 193°/193° | 196°/201° |
Подъем клапана (внутренний/наружный) | 0,482 дюйма/0,482 дюйма | 0,481 дюйма/0,481 дюйма |
Угол разделения лепестков | 116°+2 | 116°+2 |
Крепление кулачковой шестерни | 1 болт | 1 болт |
Полюса кулачковой шестерни | 4x | 4x |
Активное управление подачей топлива (AFM) | Да | Да |
Система изменения фаз газораспределения (VVT) | Нет | Да |
Клапан LC9
Характеристики клапанного механизма LC9 | |
---|---|
Тип подъемника | Гидравлический ролик |
Тип соединения подъемника | Пластиковый лоток подъемника |
Диаметр корпуса подъемника | 0,842 дюйма |
Длина толкателя | 7,385 дюйма |
Способ крепления коромысла | Подставка |
Тип коромысла | Литье под давлением, роликовая опора |
Передаточное число | 1,7 |
Смещение коромысла | Нет |
Тип пружины клапана | Улей |
Цвет пружины клапана | Натуральный |
Угол клапана | 15 градусов |
Материал впускного клапана | Сталь, сплошной шток |
Диаметр впускного клапана.![]() | 2000 дюймов |
Материал выпускного клапана | Сталь, сплошной шток |
Диаметр выпускного клапана. | 1,575 дюйма |
Тип направляющей цепи ГРМ | Подпружиненный натяжитель |
Корпус дроссельной заслонки LC9, характеристики топливной форсунки и многое другое
Годы | 2007-09 | 2010-11 |
---|---|---|
Впускной коллектор | Truck-Style | Truck-Style |
Корпус дроссельной заслонки | 87 мм, 4 болта | 87 мм, 4 болта |
Блок управления дроссельной заслонкой | Электронный привод | Электронный привод |
Номер детали топливной форсунки | 12594512 | 12613411 |
Поток топливной форсунки | 36 фунтов/ч.![]() | 37,3 фунта/ч. @ 58 фунтов на кв. дюйм |
Гибкое топливо | Да | Да |
Длина топливной форсунки между уплотнительными кольцами | 1,890 дюйма | 1,730 дюйма |
разъем топливной форсунки | ЭВ6/УСКАР | ЭВ6/УСКАР |
ПКМ | Е38 | Е38 |
Редукционное кольцо коленчатого вала | 58x | 58x |
Расположение датчика распредвала | Крышка привода ГРМ | Крышка привода ГРМ |
Масляный поддон | Зависит от применения | Зависит от применения |
Масляный насос | Большой объем (1,25 СИ на оборот) | Большой объем (1,25 СИ на оборот) |
ПРИМЕЧАНИЕ. Вы можете найти технические характеристики двигателя и подробные рекомендации по модернизации двигателя для каждого двигателя LS и Vortec на базе LS в одном месте: Полное руководство по спецификациям двигателя LS и модернизации двигателя LS .
Характеристики, диаметр цилиндра и ход поршня, головки цилиндров, характеристики кулачков и многое другое
Двигатель LMG представляет собой 5,3-литровый двигатель с железным блоком Gen. IV, который использовался в грузовиках и внедорожниках GM в период с 2007 по 2014 год. В маркетинговых целях он также был известен как Vortec 5300. Приведенная здесь информация относится к серийному двигателю LMG.
Механически похожие двигатели General Motors LS и Vortec на базе LS заведены почти на каждую ветвь генеалогического древа GM: Chevy, Pontiac, GMC, Cadillac, Buick — черт возьми, даже у Saab, Hummer и Isuzu есть некоторые ЛС любовь.
Поскольку двигатели LS и Vortec настолько распространены, они стали лучшими двигателями современной эпохи.
Эти двигатели способны развивать большую мощность и хорошо реагируют на модернизацию, такую как турбины, нагнетатели, головки блока цилиндров с высоким расходом, системы впуска, кулачки и закись азота.
[ Хотите обновить двигатель LMG? Ознакомьтесь с Руководство по обновлению двигателя LMG 5,3 л: советы экспертов по модификациям LMG для повышения производительности . ]
Рынок послепродажного обслуживания развит, доступны двигатели в ящиках , а бывшие в употреблении двигатели часто дешево закупаются на свалках.
Компания Summit Racing создала серию подробных руководств для каждого двигателя семейства LS, чтобы производители и тюнеры двигателей могли иметь удобный справочник для своих проектов.
Это специальное руководство предназначено для GM LMG 5,3 л Vortec 5300.
Дополнительные руководства по спецификациям двигателя LS и информацию, связанную с LS, можно найти здесь.
( Summit Racing Пол Сперлок и Брайан Наттер внесли свой вклад в эту статью.)
…
LMG 5.3L Vortec 5300 SpecsНоминальные характеристики двигателя | |
---|---|
Степень сжатия (2007-09) | 9,9:1 |
Степень сжатия (2010-14) | 9,6:1 |
Номинальная мощность | 310-326 л.с. |
Номинальный крутящий момент | 335–348 фут/фунт. |
Приложения LMG
Восьмая цифра VIN | Год | Марка | Модель |
---|---|---|---|
0 | 2007-13 | Шевроле | Лавина |
0 | 2007-13 | Шевроле | Сильверадо |
0 | 2007-13 | GMC | Сьерра |
0 | 2007-14 | Шевроле | Пригородный |
0 | 2007-14 | Шевроле | Тахо |
0 | 2007-14 | GMC | Юкон |
Блоки двигателя LMG
Характеристики блока цилиндров LMG | |
---|---|
Литейные номера | 12576177, 12576178, 1589779 |
Материал | Железо |
Рабочий объем | 5,3 л / 325 c.![]() |
Диаметр отверстия | 3,780 дюйма |
Ход | 3,622 дюйма |
Высота платформы | 9,240 дюйма |
Расстояние между отверстиями | 4,400 дюйма |
Расположение упорного подшипника | #3 Основной |
Основная крышка, тип | 6 болтов |
Диаметр отверстия основного корпуса. | 2,751 дюйма |
Диаметр отверстия корпуса кулачка. | Отверстие 1/5 = 2,346, Отверстие 2/4 = 2,326, Отверстие 3 = 2,307 |
Осевая линия кулачка и кривошипа | 4,914 дюйма |
Вращающийся узел LMG
Технические характеристики вращающегося узла LMG | |
---|---|
Материал поршня | Заэвтектический литой алюминиевый сплав |
Поршневой тип (2007-09) | Плоский верх |
Поршневой тип (2010-14) | Плоский верх с предохранительным клапаном |
Объем поршня (2007-09) | 0cc |
Объем поршня (2010-14) | +3cc |
Диаметр штифта для запястья.![]() | 0,9431 дюйма (полностью плавающий) |
Материал шатуна | Металлический порошок |
Тип шатуна | Двутавровая балка |
Длина шатуна | 6,098 дюйма |
Отверстие корпуса шатуна | 2,225 дюйма |
Болты шатуна | M9 x 1 x 43 |
Номер отливки шатуна (последние 3 цифры) | 143 |
Материал коленвала | Чугун |
Номер отливки коленчатого вала (последние 3 цифры) | 216 |
Коренная шейка коленчатого вала | 2,559 дюйма |
Шейка коленчатого вала | 2,100 дюйма |
Редукционное колесо | 58x |
Головки цилиндров LMG
Характеристики головки блока цилиндров LMG | |
---|---|
Литейные номера | 799, 243 |
Материал | Алюминий |
Объем камеры сгорания | 65cc |
Форма впускного отверстия | Собор |
Объем впускного патрубка | 210 куб.![]() |
Форма выпускного отверстия | D-образное отверстие |
Объем выхлопной трубы | 75cc |
Диаметр впускного клапана | 2000 дюймов |
Диаметр выпускного клапана | 1,575 дюйма |
Тип болта головки блока цилиндров | Момент до предела текучести (TTY) |
Размер болта головки блока цилиндров | (10) M11 x 2 x 100, (5) M8 x 1,25 x 45 |
Характеристики распределительного вала LMG
Характеристики распределительного вала LMG | ||
---|---|---|
Годы | 2007-09 | 2010-14 |
Номер детали | 12593207 | 12625436 |
Длина @ 0,050 дюйма (внутр.![]() | 193°/193° | 196°/201° |
Подъем клапана (внутренний/наружный) | 0,482 дюйма/0,482 дюйма | 0,481 дюйма/0,481 дюйма |
Разделение лепестков | 116° | 116°+2 |
Крепление кулачковой шестерни | 1 болт | 1 болт |
Полюса кулачковой шестерни | 4x | 4x |
Активное управление подачей топлива (AFM) | Да | Да |
Система изменения фаз газораспределения (VVT) | Нет | Да |
Клапанный механизм LMG
Характеристики клапанного механизма LMG | |
---|---|
Тип подъемника | Гидравлический ролик |
Тип соединения подъемника | Пластиковый лоток подъемника |
Диаметр корпуса подъемника | 0,842 дюйма |
Длина толкателя | 7,385 дюйма |
Способ крепления коромысла | Подставка |
Тип коромысла | Литье под давлением, роликовая опора |
Передаточное число | 1,7 |
Смещение коромысла | Нет |
Тип пружины клапана | Улей |
Цвет пружины клапана | Натуральный |
Угол клапана | 15 градусов |
Материал впускного клапана | Сталь – сплошной шток |
Диаметр впускного клапана.![]() | 2000 дюймов |
Материал выпускного клапана | Сталь – сплошной шток |
Диаметр выпускного клапана. | 1,575 дюйма |
Другие ключевые характеристики LMG
Корпус дроссельной заслонки, топливные форсунки, масляный поддон Технические характеристики и многое другое | |
---|---|
Впускной коллектор | Грузовой автомобиль |
Корпус дроссельной заслонки | 87 мм, 4 болта |
Блок управления дроссельной заслонкой | Электронный (Drive-by-Wire) |
Номер детали топливной форсунки | 12613411 |
Поток топливной форсунки | 32 фунта/ч.![]() |