Производство масел — Технология масел моторных
|
Производство моторного масла — РусТоргОйл
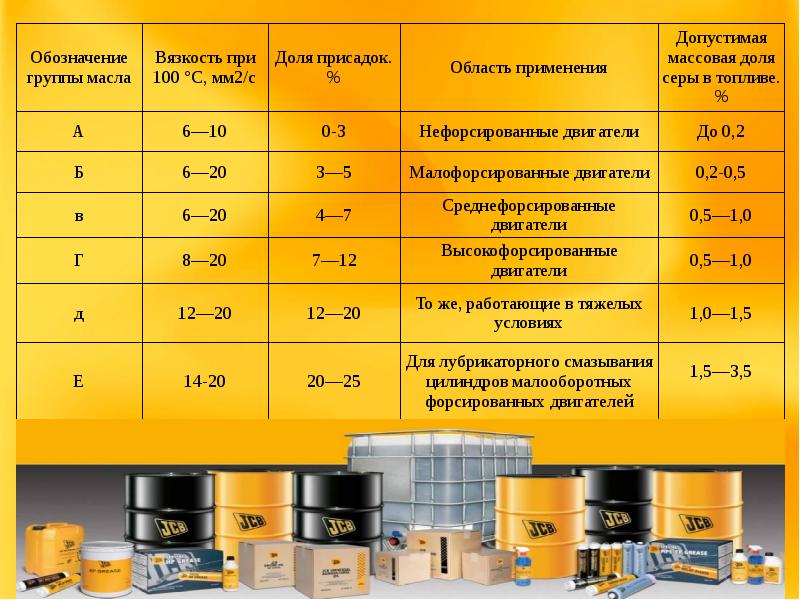
Процесс производства смазочных масел для современной моторной техники состоит из трёх этапов:
- 1. Подготовка сырья — получение исходных масляных фракций
Базовые масла (компоненты масел) производятся на технологических установках переработки нефти по существующим поточным схемам. На установках производится перегонка нефти с получением дистиллятных масляных фракций 350-420°С, 420-500°С и фракции выше 500°С. В настоящий момент развитие нефтеперерабатывающей промышленности позволяет производить перегонку с более узким фракционным составом получая большее количество базовых масел.
- 2. Получение компонентов масел из исходных масляных фракций путем реализации различных способов очистки фракций на установках маслоблока
В большинстве случаев это селективная очистка масляных фракций 350-420°С и 420-500°С фурфуролом с получением рафинатов фракций 350-420 и 420-500°С. Деасфальтизация гудрона пропаном и селективная очистка смесью фенола и трикрезола (растворитель «селекто») деасфальтизата в растворе пропана с получением остаточного рафината фракции выше 500°С. Гидроочистка остаточного рафината фракции выше 500°С в стационарном слое катализатора с выработкой остататочного гидроочищенного рафината фракции выше 500°С. Депарафинизация рафинатов фракций 350-420°С и 420-500°С и остаточного гидроочищенного
рафината в растворе метилэтилкетон-толуол с получением депарафинированных масляных фракций 350-420°С и 420-500°С, а также остаточного компонента гидроочищенного ( базовое масло ОБ-500).
- 3. Непосредственное получение товарных масел смешением (компаундированием) масляных компонентов и присадок.
Все процессы производства смазочных масел включают ступени регулирования вязкости базового масла путем компаундирования и введения присадок с получением продуктов с заданными свойствами. Масла обычно компаундируют при 50—60 °С. При этой температуре вязкость масел и присадок достаточно низки для гарантированного удовлетворительного и быстрого перемешивания. В то же время базовые масла и присадки не подвергаются значительным термическим воздействиям. Но при высоких температурах, например 100 °С, скорости разложения некоторых присадок (в частности, противозадирных) уже значительны. Температуры выше 100—120 °С требуются лишь в случае присадок, трудно поддающихся растворению, например сера в смазочно-охлаждающих жидкостях.
Масла можно компаундировать периодически в резервуарах, реакторах и смесителях или непрерывно на соответствующих установках.
При периодическом компаундировании резервуары для компаундирования или смесители, емкостью от 1 до 20 м3, обычно обогреваются и снабжены мешалками. Количество компонентов определяют по массе, объему или дозируют с помощью дозировочного насоса. Оптимальное перемешивание достигается с помощью пропеллерных мешалок, так как медленно вращающиеся лопастные мешалки не обеспечивают необходимой интенсивности перемешивания. При использовании циркуляционного насоса его мощность должна быть достаточной для многократной циркуляции всего объема масла со скоростью несколько оборотов в час.
Старый способ перемешивания воздухом, подаваемым в резервуар для компаундирования, экономически оправдан в тех случаях, когда при температурах смешения отсутствует опасность окисления компонентов масла. В этом случае целесообразно воздух подавать в резервуар не из центральной системы, а снабдить резервуар собственной воздуходувкой. В противном случае возможны осложнения из-за конденсированной воды или масляного тумана, увлеченного сжатым воздухом.
Поточное смешение — непрерывное компаундирование является единственным экономически оправданным способом компаундирования больших объемов товарных масел. В этом процессе все компоненты, базовые масла и присадки, дозируют в основной поток, в так называемую линию смешения. В системе Корнелла применяют два или более синхронно работающих дозировочных насоса, объемную производительность которых можно с высокой точностью регулировать автономно. Для бесперебойной работы требуется свободный доступ компонентов смешения к дозировочным насосам. В пропорциональных системах применяют раздельные дозаторы для каждого компонента. Вращение дозаторов сопряжено с коническими шестернями, соединенными с планетарными шестернями. Требуемая скорость дозирования достигается, когда планетарные шестерни дозаторов эталонного и контролируемого компонентов вращаются с одинаковой скоростью.
Любое отклонение от заданного соотношения приводит к неравномерности движения ведомых шестерен, в результате чего изменяется положение планетарной шестерни и, следовательно, изменяется скорость подачи компонентов. Преимущество этой системы заключается в том, что в случае отклонения от заданной композиции автоматически отключается вся аппаратура.
В настоящее время количество индивидуальных компонентов измеряют и регулируют с помощью электронных устройств. Многие эксплуатируемые установки для компаундирования масел полностью автоматизированы. Впервые такая установка («Блендомат») была применена в 1962 г. для компаундирования моторных бензинов с использованием двух базовых компонентов и трех присадок. Число компонентов может изменяться.
Высокие требования, предъявляемые к эксплуатационным свойствам смазочных масел, частично достигаются подбором сырья и соответствующей очисткой исходных масляных фракций. Введение в масла в процессе компаундирования присадок, достигаются необходимые эксплуатационные свойства масел.
Эффективность присадок в маслах различного происхождения значительно зависит от оптимальной концентрации, а в случае композиции (пакета) присадок – также от оптимального сочетания компонентов.
Для получения сбалансированных композиций моторных масел отвечающих комплексу требований, смеси масел смешивают с антиокислительными, моюще-диспергирующими, противоизносно-противозадирными, депрессорными, вязкостными и антипенными присадками. Также при производстве возможно использование многофункциональных пакетов присадок включающие в себя все вышеперечисленные свойства.
Как завод становится моторным маслом
Выбор местоположения
Свяжитесь с нами Гарантия Шеврон SDS/PDS
США — английский
В другом месте? Выберите свое местоположение
US
Английский
Belarus
Российский
Bulgaria
Bulgarian
Канада
Englishfrench
Кипр
Грек
CZECH
CZECH0012 Czech
Europe
English
France
French
Germany
Germany
Greece
Greek
Hungary
Hungarian
Italy
Italian
Kazakhstan
Russian
Middle East & Africa
Английский
Нидерланды
Голландский
Польша
Польский
Румыния
Румынский
Россия
Russian
Saudi Arabia
English
Serbia
Serbian
South Africa
English
Spain
Spanish
Sweden
Swedish
Turkey
Turkish
Uzbekistan
Russian
Создание возобновляемого полностью синтетического материала Havoline® PRO-RS™
Наступила эра автомобильных смазочных материалов на основе возобновляемых источников энергии. 1 ноября Chevron выпустила возобновляемое полностью синтетическое моторное масло Havoline® PRO-RS™ — наш первый продукт, на 25% состоящий из растительных масел, полученных из экологически чистых источников. Естественно, мы уже слышим вопрос: «Как ты это сделал?» Как растительное вещество превращается в высокоэффективное моторное масло?
Все начинается с солнца. Растения поглощают солнечные фотоны, углекислый газ из атмосферы и другие питательные вещества из почвы. Они, в свою очередь, образуют триглицериды, которые хранятся в семенах и мякоти растений и могут быть переработаны в масло. Само по себе это не новая концепция — например, именно так производятся растительные масла. Что нового в этом растительном масле, так это его исключительная чистота и однородность молекулярной структуры. Эти свойства обеспечивают важные преимущества, такие как более низкая летучесть и трение, что делает его идеальным для разработки синтетических моторных масел следующего поколения, таких как Havoline PRO-RS.
Havoline PRO-RS — первое масло, произведенное с использованием технологии Chevron ECOSTRENGTH, которая сочетает в себе возобновляемое растительное сырье с традиционным синтетическим базовым маслом и пакетом присадок для получения смазочного материала со всеми эксплуатационными характеристиками полностью синтетического масла премиум-класса. . Наше сырье на растительной основе обычно не содержит примесей, присутствующих в традиционных базовых маслах, получаемых из сырой нефти, а его сырье является возобновляемым ресурсом. Благодаря тому, что масло на растительной основе составляет 25 % готовой смазки, Havoline PRO-RS соответствует критериям, чтобы быть названным продуктом на биологической основе, сертифицированным Министерством сельского хозяйства США.
Понимая, как мы пришли к этому обозначению, следующий вопрос, который мы слышим, звучит так: «Он работает так же хорошо, как полностью синтетический материал, производимый традиционным способом?» Ответ: да, работает так же хорошо, а в некоторых случаях и лучше. Оно обеспечивает моющую способность, защиту от износа и температурную стабильность, которые вы ожидаете от синтетического моторного масла. Оно также демонстрирует превосходное «сохранение экономии топлива», что означает, что экономия топлива от свежего масла сохраняется дольше, чем у обычных полностью синтетических или обычных моторных масел, которые могут быстрее разлагаться и заставлять двигатель работать с большей нагрузкой по мере старения масла в процессе эксплуатации. .
Успешное применение возобновляемого сырья, полученного из устойчивых источников, в моторном масле для легковых автомобилей — это огромный шаг к будущему с низким уровнем выбросов углерода. И это отвечает растущему потребительскому спросу на продукты с меньшим воздействием на окружающую среду. Такой продукт, как Havoline PRO-RS, показывает нам, насколько далеко продвинулась наука о рафинировании растительного масла, и дает нам наглядное представление о возможностях по мере того, как технология продолжает развиваться.
30.11.2021
метки:
Havoline
,
Синтетическое масло
,
возобновляемые
,
Pro-RS
,
Jimm Smiley, менеджер по потребительскому сектору, America’s Fuels and Lubricants. Джим Смайли — менеджер потребительского сектора, отвечающий за управление брендами Havoline и Techron. До прихода в Chevron Джим руководил управлением брендами и продуктами в Intuit, Yahoo!, DuPont и нескольких стартапах. Он получил степень бакалавра наук в области финансов в Университете Санта-Клары и степень магистра делового администрирования в Джорджтаунском университете.
Фильтр по
Очистить все
Категория
Возобновляемый
PRO-RS
Havoline
Синтетическое масло
Применить фильтр Очистить все
Смазочное производство | Hydrocarbon Engineering
Согласно последним прогнозам, мировой рынок смазочных материалов ежегодно растет примерно на 4% и может достичь общей стоимости в 166 миллиардов долларов США в 2025 году. На Рисунке 1 представлена тенденция роста на рынке смазочных материалов. 1 Высокая добавленная стоимость смазочных материалов по сравнению с транспортным топливом, сопровождаемая тенденцией снижения спроса на транспортное топливо, указывает на привлекательную альтернативу для нефтепереработчиков с соответствующим оборудованием для повышения их доходов и конкурентоспособности на рынке переработки. Текущий экономический кризис из-за пандемии COVID-19 повлиял на рынок смазочных материалов, но в меньшей степени, чем на транспортное топливо.
Рисунок 1. Тенденция роста спроса на смазочные материалы. 1
Как и в случае других производных сырой нефти, экономический и технологический прогресс потребовал производства смазочных масел более высокого качества и производительности, а также, что важно, с более низким содержанием загрязняющих веществ.
Основными требованиями к качеству смазочных масел являются вязкость, температура вспышки, индекс вязкости (изменение вязкости в зависимости от температуры), точка текучести, химическая стабильность и летучесть.
По данным Американского института нефти (API) смазочные базовые масла можно классифицировать, как показано в таблице 1. Смазочные масла из групп II, III и IV имеют более высокое качество, чем базовые масла из группы I; значительно снижено содержание таких примесей, как сера и ненасыщенные соединения и, кроме того, индекс вязкости выше для этих групп.
Таблица 1.
Маршруты производства смазочных материалов
Первым этапом процесса производства смазочных материалов является вакуумная перегонка полученного атмосферного остатка, такого как кубовый продукт в процессах атмосферной перегонки. Для установок вакуумной перегонки, предназначенных для производства смазочных фракций, фракционирование требует большего контроля, чем в установках, предназначенных для преобразования газойлей в топливо. 2 Цель состоит в том, чтобы избежать термического разложения и контролировать кривую дистилляции боковых потоков. Вторичная вакуумная дистилляционная колонна необходима, когда желательно отделить поток тяжелого нейтрального масла от вакуумного остатка.
В установках по производству смазочных материалов, основанных на использовании растворителя, следующие этапы, по сути, представляют собой процессы физического разделения с целью удаления из технологических потоков компонентов, которые могут ухудшить желаемые свойства базовых масел, в основном индекс вязкости и химическую стабильность .
На рис. 2 показана блок-схема, соответствующая стадиям процесса производства базовых смазочных масел путем экстракции растворителем.
Рис. 2. Технологическая схема производства базовых смазочных масел сольвентным способом.
Как упоминалось ранее на этапе вакуумной дистилляции, качество фракционирования, полученное между фракциями, имеет решающее значение для достижения этими потоками требований к качеству, таких как температура вспышки и вязкость. После этапа вакуумной перегонки боковые фракции перекачиваются в установку экстракции ароматических соединений, а вакуумный остаток направляется в установку деасфальтизации пропана. Процесс деасфальтизации пропаном направлен на удаление из вакуумного остатка более тяжелых фракций, которые можно применять в качестве смазочного масла. В установках пропановой деасфальтизации, предназначенных для производства смазочных масел, в качестве растворителя используется чистый пропан, так как этот растворитель обладает более высокой селективностью по удалению смол и асфальтенов из деасфальтизируемого масла.
На стадии экстракции ароматических соединений технологические потоки контактируют с растворителями, избирательно удаляющими ароматические соединения, в основном полиароматические соединения. Главной задачей при удалении этих соединений является то, что они имеют низкий индекс вязкости и низкую химическую стабильность, что крайне нежелательно в смазочных маслах. Поскольку соединения азота и серы обычно присутствуют в полиароматических структурах, на этой стадии удаляется основная часть серы и азота, содержащихся в технологическом потоке. Растворителями, обычно применяемыми в процессе экстракции ароматических соединений, являются фенол, фурфурол и N-метилпирролидон.
Следующим этапом является удаление линейного парафина с высокой молекулярной массой путем экстракции растворителем. Этот шаг важен, потому что эти соединения препятствуют течению смазочного масла при низких температурах. Типичным растворителем, используемым в установке депарафинизации растворителем, является метилизобутилкетон (МИК), но некоторые технологические установки применяют для этой цели толуол и/или метилэтилкетон (МЭК).
После удаления парафина смазочное масло направляется на финишную обработку. На этом этапе соединения гетероатома (кислород, сера и азот) удаляются. Эти соединения могут придать смазочному маслу цвет и химическую нестабильность. Некоторые оставшиеся полиароматические молекулы также удаляются. Некоторые перерабатывающие заводы с небольшими капиталовложениями и перерабатывающими мощностями применяют на этом этапе обработку глиной. Однако современные заводы и заводы с более высокой мощностью переработки используют установки мягкой гидроочистки; это особенно важно, когда нефть, обработанная с более высоким содержанием загрязняющих веществ, в данном случае глинистый слой, очень быстро насыщается.
Парафин, удаленный из смазочных масел, обрабатывается для удаления избыточного масла в блоке, называемом блоком удаления парафина. На этом этапе технологический поток подвергают воздействию пониженных температур для удаления низкоразветвленного парафина, который имеет низкую температуру плавления. Как и в случае со смазочными маслами, следующий этап представляет собой завершающий процесс для удаления гетероатомов (N, S, O) и насыщения полиароматических соединений. В случае парафина, как правило, процесс гидроочистки применяется с достаточной жесткостью, чтобы насытить ароматические соединения, что может обеспечить достижение пищевого качества конечного продукта. Как упоминалось ранее, способ растворения позволяет производить смазочные масла группы I. Однако смазочные масла, используемые в тяжелых условиях работы (большой перепад температур), должны иметь более высокое содержание насыщенных соединений и более высокий индекс вязкости. В этом случае необходимо применить способ гидроочистки. Серьезным ограничением в производстве смазочных материалов с помощью растворителя является необходимость использования парафиновой сырой нефти, что, как правило, связано с более высокими затратами и снижает эксплуатационную гибкость нефтеперерабатывающих заводов, особенно в отношении поставок сырой нефти в случае геополитического кризиса.
Несмотря на важные стратегические вопросы, такие как цены на сырую нефть и поставки, смазочные масла группы I имеют тенденцию быстро терять рынок из-за их низкой эффективности по сравнению с остальными группами, особенно с учетом растущего технологического развития автомобильной промышленности. 3 Этот факт является одной из наиболее важных движущих сил для капитальных вложений, направленных на повышение мощности нефтеперерабатывающего оборудования для производства высококачественных смазочных масел путем гидроочистки. Другим существенным фактором, негативно влияющим на конкурентоспособность нефтеперерабатывающих заводов, полагающихся исключительно на растворитель, является то, что смазочные масла групп I и II в последние годы утратили свои позиции на рынке, в основном в связи с технологическими требованиями новейших автомобильных двигателей. прогноз изменения доли рынка различных видов базовых масел на рынке.
Рисунок 3. Распределение рынка базовых масел. 5
Согласно данным, представленным на рис. 3, ожидается значительное снижение спроса на базовые масла группы I, что приведет к большим потерям в конкурентоспособности нефтеперерабатывающих заводов, полагающихся на производство базовых масел исключительно сольвентными способами.
Путь гидроочистки
При производстве смазочного масла путем гидроочистки физические процессы заменяют каталитические процессы, в основном процессы гидрообработки. На рис. 4 показана блок-схема технологической последовательности производства базовых смазочных масел путем гидроочистки.
Рисунок 4. Технологическая схема получения базовых смазочных масел по схеме гидроочистки.
В этом случае фракционирование на этапе вакуумной дистилляции более гибко, чем на пути с растворителем, поскольку потоки будут подвергаться крекингу в установке гидрокрекинга, поэтому необходим еще один этап дистилляции.
После стадий вакуумной перегонки и пропановой деасфальтизации технологические потоки направляются на установку гидроочистки. Этот этап направлен на насыщение полиароматических соединений и удаление загрязняющих примесей, таких как сера и, прежде всего, азот, который является сильным дезактивирующим агентом для катализатора гидрокрекинга. 4
На стадии гидрокрекинга сырьевой поток подвергается крекингу в контролируемых условиях, и происходят химические реакции, такие как дегидроциклизация и насыщение ароматическими соединениями, что придает технологическому потоку адекватные характеристики для их применения в качестве смазочных материалов.
Следующая стадия, гидроизомеризация, направлена на ускорение изомеризации линейного парафина (что может снизить индекс вязкости) путем получения разветвленного парафина.
После гидроизомеризации технологический поток перекачивается на установки гидроочистки для насыщения оставшихся полиароматических соединений и удаления гетероатомов. На этапе гидроочистки содержание воды в смазочном масле контролируется, чтобы избежать помутнения конечного продукта.
При сравнении маршрутов производства смазочных материалов можно заметить, что маршрут гидроочистки обеспечивает большую гибкость в отношении перерабатываемой нефти. Как упоминалось ранее, так как растворитель использует в основном физические процессы, необходимо выбирать для переработки сырую нефть с более высоким содержанием парафина и низким содержанием загрязняющих веществ (в основном азота). Другим недостатком сольвентного маршрута является применение растворителей, которые могут нанести ущерб окружающей среде и требуют особых требований безопасности во время обработки. Производство потоков с низкой добавленной стоимостью, таких как ароматический экстракт, является еще одним недостатком.
Бразильский рынок смазочных материалов
Парафиновые масла на внутреннем рынке Бразилии снабжаются нефтеперерабатывающими заводами, применяющими сольвентный способ с этапом гидроочистки для производства смазочных масел и парафинов для различных потребителей, в том числе для пищевой и косметической промышленности. Производство смазочных материалов в стране в 2019 году составило 3,5 млн баррелей. Кроме того, внутренний рынок также снабжается некоторыми импортерами. По данным Бразильского нефтяного агентства (ANP), внутреннее потребление смазочных масел в 2019 году достигло 7,7 млн баррелей.. На Рисунке 5 представлена структура бразильского рынка смазочных масел в 2019 г.
Рис. 5. Баланс бразильского рынка смазочных масел в 2019 г. (по данным ANP).
В случае Бразилии значительная часть рынка приходится на переработанное смазочное масло. Переработка или повторная очистка отработанного смазочного масла выполняет двойную роль: устранение опасных остатков и снижение необходимости извлечения большего количества нефти для производства базовых смазочных масел. Промышленные процессы, применяемые для регенерации отработанного смазочного масла, называются: кислотно-глинистый процесс (процесс Мейкена), процесс деасфальтизации с помощью пленочных испарителей и способ гидрообработки, который позволяет производить базовые масла более высокого качества (например, группы II и III). ). Некоторые исследователи посвятили свои усилия разработке новых технологий повторной очистки отработанных смазочных масел, и некоторые из этих технологий оказались многообещающими, например, ультрафильтрация в мембранах. Однако технология все еще находится на начальной стадии разработки.
По данным ANP, в Бразилии почти 40% потребляемого смазочного масла восстанавливается и направляется на переработку на перерабатывающих заводах. Несмотря на эти важные данные, бразильское производство смазочных масел сосредоточено на маслах Группы I и II.
Заключение
Как уже говорилось, несмотря на высокие капиталовложения в установки гидроочистки, более высокая добавленная стоимость смазочных материалов групп II и III и растущий рынок могут оправдать инвестиции, особенно с учетом тенденции сокращения транспортных топлив. спрос на глобальном уровне в среднесрочной перспективе. Это побудило нефтепереработчиков искать способы обеспечения доли рынка и доходов в перерабатывающей промышленности за счет максимизации производных с высокой добавленной стоимостью на растущих рынках нефтехимии и смазочных масел. Ожидается, что в связи с ускоренным развитием технологий, особенно на автомобильном рынке, смазочные масла группы I потеряют свою долю на рынке в ближайшие годы. Это побуждает переработчиков искать капиталовложения для поддержания своей конкурентоспособности на рынке смазочных материалов. Другим побочным эффектом для производителей смазочных материалов, использующих платежеспособные маршруты, является увеличение импорта для снабжения внутреннего рынка, что приводит к внешней зависимости важнейших производственных ресурсов, а также к негативным последствиям для платежного баланса.
Ссылки
- БАУ, А., БРУНИ, Г., ХАССИН, Л., КЬЮЭЛЛ, Д., КОЛЕР, Б. и ВЕРИТИ, Р., «Возможности роста производства смазочных материалов сохраняются, несмотря на переход на электромобили», McKinsey & Компания (7 декабря 2018 г.).
- ГЭРИ, Дж. Х.; HANDWERK, GE, «Нефтепереработка – технология и экономика», издание 4 th , Marcel Dekker, (2001).
- «Отчет об анализе размера рынка смазочных материалов, доли и тенденций по продуктам (промышленные, автомобильные, морские, аэрокосмические), по регионам и прогнозу по сегментам, 2019 г.